Highly Fatigue-Resistant FMS Alloy with Enhanced Weldability
—Welded Beams with X-Shaped Cross-Sections May Be Used to Increase the Ability of Seismic Dampers to Withstand Heavy Loads and Absorb Long-Period Ground Motion—
2021.03.10
National Institute for Materials Science (NIMS)
NIMS enhanced the weldability of the previously developed fatigue-resistant FMS (iron-manganese-silicon-based) alloy, designed for use in seismic dampers, alloy, designed for use in seismic dampers, without compromising its fatigue durability by modifying its composition.
(”Development of ferrous-based weldable seismic damping alloy with prolonged plastic fatigue life” Fumiyoshi Yoshinaka, Takahiro Sawaguchi, Susumu Takamori, Terumi Nakamura, Goro Arakane, Yasuhiko Inoue, Susumu Motomura, Atsumichi Kushibe; Journal: Scripta Materialia, Volume 197, 113815 [February 24, 2021]; DOI : 10.1016/j.scriptamat.2021.113815)
Abstract
- NIMS enhanced the weldability of the previously developed fatigue-resistant FMS (iron-manganese-silicon-based) alloy, designed for use in seismic dampers, alloy, designed for use in seismic dampers, without compromising its fatigue durability by modifying its composition. As a result, separate pieces of this alloy can now be welded together without causing cracks. The alloy may be processed into beams with H- or X-shaped cross-sections, which can be used to improve seismic dampers’ ability to withstand heavy loads.
- Steel seismic dampers are used to reduce the shaking of buildings during earthquakes by converting seismic energy into thermal energy through the elasto-plastic deformation mechanism. Long-period ground motion induced by the Great East Japan Earthquake caused serious damage across large areas of Japan. This prompted NIMS, Takenaka Corporation and Awaji Materia to jointly develop a seismic damper capable of withstanding repeated elasto-plastic deformation over a long period of time. This project produced an FMS alloy with a fatigue durability 10 times that of conventional materials used in seismic dampers. FMS alloy plates were integrated into the cores of shear panel dampers, which were then installed in the JP Tower Nagoya, a skyscraper, in 2014. The joint team then developed a welding technique to join FMS alloy pieces and weldable steel pieces and incorporated these welded products into brace-type seismic dampers. These dampers were then installed in Aichi Sky Expo, one of the largest exhibition centers in Japan, in 2018. This research was conducted to improve the weldability of the FMS alloy so that multiple pieces of it can be welded together to form beams with large H- or X-shaped cross-sections without causing hot cracks (solidification cracks) in the welded portions. The use of these beams as the core component of brace-type seismic dampers is expected to improve the dampers’ ability to withstand the heavy loads experienced by large-scale buildings.
- This NIMS research team has developed a second-generation FMS alloy with high fatigue durability and resistance to hot cracking (solidification cracking) by modifying the composition of the first-generation FMS alloy. The team made a slight adjustment to the alloy’s nickel-chromium ratio. These modifications enabled the alloy to undergo reversible deformation at room temperature, made the alloy’s crystalline structure more resistant to welding-induced cracking and gave the welded portions very high fatigue durability. Experiments have confirmed that the fatigue life of the second-generation alloy is equivalent to that of the first-generation alloy and that welding it does not cause cracks.
- These successes led to the 2020 launch of a new research project to create structures and structural components by welding second-generation FMS alloy pieces together (under the project title “Development of a high-load-capacity brace-type seismic damper by welding highly fatigue resistant alloys” (project leader: Yasuhiko Inoue, Chief Researcher, Takenaka Corporation) supported by the industry-academia collaborative R&D category of the Adaptable and Seamless Technology Transfer Program through Target-driven R&D (A-STEP) run by the Japan Science and Technology Agency (JST)). Through this project, we plan to process the second-generation FMS alloy into welded beams with large H- or X-shaped cross-sections and incorporate them into the cores of seismic dampers.
- This project was carried out by a research team led by Takahiro Sawaguchi (Leader of the Vibration Control Materials Group, Research Center for Structural Materials (RCSM), NIMS) and Terumi Nakamura (Leader of the Welding and Joining Technology Group, RCSM, NIMS).
- This research was published in the online version of Scripta Materialia on February 24, 2021.
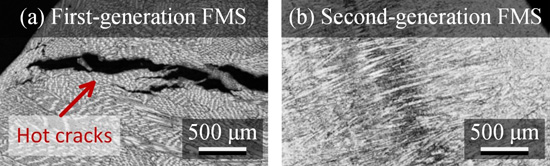
Figure. Microstructures of the welded portions of the (a) first-generation and (b) second-generation FMS alloys
Related files
- Research Center for Structural Materials(RCSM)
Contact information
(Regarding this research)
-
Takahiro Sawaguchi
Group Leader
Vibration Control Materials Group
Design and Producing Field
Research Center for Structural Materials
National Institute for Materials Science
Tel: +81-29-859-2416
E-Mail: SAWAGUCHI.Takahiro=nims.go.jp
(Please change "=" to "@") -
Terumi Nakamura
Group Leader
Welding and Joining Technology Group
Bonding and Manufacturing Field
Research Center for Structural Materials
National Institute for Materials Science
Tel: +81-29-859-2113
E-Mail: NAKAMURA.Terumi=nims.go.jp
(Please change "=" to "@")
(General information)
-
Public Relations Office
National Institute for Materials Science
Tel: +81-29-859-2026, Fax: +81-29-859-2017
E-Mail: pressrelease=ml.nims.go.jp
(Please change "=" to "@")