Exoskeletal Microstructure of Extremely Hard Coconut Crab Claws
—3D Imaging of Internal Pincer Structures May Provide Insights into the Development of Tough, Lightweight Materials—
2021.05.24
National Institute for Materials Science (NIMS)
Okinawa Churashima Foundation Research Center
The NIMS Research Center for Structural Materials and the Okinawa Churashima Foundation Research Center jointly ascertained the microstructure and chemical composition of the extremely tough exoskeletons of coconut crab claws, which are capable of generating a stronger pinching force than those of any other crustacean.
Abstract
- The NIMS Research Center for Structural Materials and the Okinawa Churashima Foundation Research Center jointly ascertained the microstructure and chemical composition of the extremely tough exoskeletons of coconut crab claws, which are capable of generating a stronger pinching force than those of any other crustacean. They also succeeded in creating three-dimensional images of the claws’ complex exoskeletal tissue structures.
- The coconut crab—a hermit crab that has evolved to abandon shell-carrying behavior—is one of the largest terrestrial crustaceans. Its populations have seriously declined globally, and in Japan, they inhabit only the areas surrounding Okinawa Prefecture. During the course of its evolution, the coconut crab developed an armor-like exoskeleton to protect itself from natural enemies and lost the ability to fit into empty seashells. Although some Okinawan regions traditionally eat coconut crabs, they are known to have much harder exoskeletons than other edible crustaceans, such as the opilio crab (Chionoecetes opilio) and the red king crab (Paralithodes camtschaticus). The coconut crab was featured as a dangerous creature in “72 Dangerous Animals: Asia,” a Netflix-distributed nature documentary series. The crab has a pinching force that equals or exceeds 90 times its body weight, one of the highest values recorded among living organisms. In addition, the pinching force of a fully-grown 4 kg coconut crab is approximately 360 kg, which is equivalent to the biting force of a lion. It was unknown, however, how the exoskeleton of a coconut crab claw can be both lightweight and able to withstand such strong force without breaking.
- To find an answer to this question, this research team investigated the exoskeletal tissues and microstructures of the claws of coconut crabs weighing approximately 1 kg, measured the composition and hardness of the exoskeleton at different depths and created 3D images of the complex, microscopic laminated structures (i.e., twisted plywood-like structures) within the exoskeleton. The main findings are as follows:
- The outer surface of the claw is as hard as steel.
- The thin, hard, calcified outer layer is composed of stacks of approximately 100 microscopic plates with gradually twisting horizontal orientations. This structure makes the hard outer layer resistant to collapse even when some of the plates are damaged.
- The porous inner layer of the exoskeleton is softer than the outer layer and is capable of absorbing external force, protecting the claw from damage.
- 3D images of these structures at different depths within the exoskeleton were created for the first time using state-of-the-art microscopes and techniques designed for materials engineering.
- A great deal of effort has been made to develop structural materials that are both light and tough. Understanding the exoskeletal structure of coconut crab claws—which are light and capable of withstanding the strongest pinching force among crustaceans—may provide helpful insights into the development of these materials. Such materials may potentially be used in vehicle (e.g., automobile and aircraft) components, reducing carbon dioxide emissions. In addition, these materials may be applicable to the development of small medical devices, such as strong, small-diameter forceps with very strong gripping force.
- This project was carried out mainly by a research team led by Tadanobu Inoue (Group Leader, Research Center for Structural Materials (RCSM), NIMS), Toru Hara (Group Leader, RCSM, NIMS) and Shin-ichiro Oka (Chief Research Scientist, Okinawa Churashima Foundation Research Center). This work was funded by the NIMS support system for curiosity-driven research (FY2019 program for enhancing proposal ability) and a FY2020 research grant provided by the Uehara Memorial Foundation.
- This research was published in Materials & Design, an open access journal, on April 28, 2021.
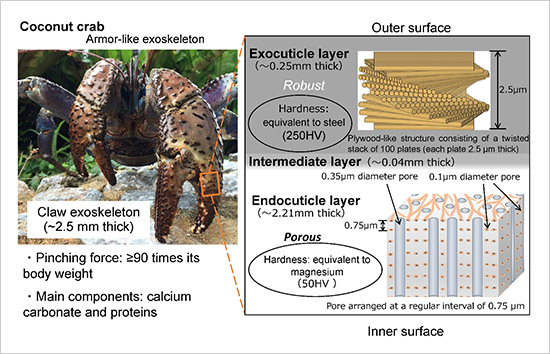
Figure. Schematic diagram showing the cross-sectional structures of the coconut crab claw exoskeleton
Related files
- Research Center for Structural Materials(RCSM)
Contact information
(Regarding this research)
-
Tadanobu Inoue
Field Director
Plasticity Processing Group
Design and Producing Field
Research Center for Structural Materials
National Institute for Materials Science
Tel: +81-29-859-2148
E-Mail: INOUE.Tadanobu=nims.go.jp
(Please change "=" to "@") -
Shin-ichiro Oka
Zoological Laboratory
Okinawa Churashima Foundation Research Center
Tel: +81-980-48-2266
E-Mail: sh-oka=okichura.jp
(Please change "=" to "@")
(General information)
-
Public Relations Office
National Institute for Materials Science
Tel: +81-29-859-2026
Fax: +81-29-859-2017
E-Mail: pressrelease=ml.nims.go.jp
(Please change "=" to "@") -
Project Planning & Public Relationship Department
Okinawa Churashima Foundation
Tel: +81-980-48-3649
Fax: +81-980-48-3122
E-Mail: oki-pr=okichura.jp
(Please change "=" to "@")