ZnO-Coated High-Performance Bearings Developed
—They Reduce Friction by about One-Third. Playing a Vital Role in a Newly Developed Small Jet Engine Generator for Emergency Use—
2016.06.08
(2016.08.24 Update)
National Institute for Materials Science (NIMS)
Tohoku University
Fox Corporation Ltd.
A research group consisting of NIMS and Tohoku University developed a coating technique using a zinc oxide (ZnO) material, an environment-friendly, low-friction material developed exclusively by NIMS. When bearing balls were coated with the ZnO material, the material’s low frictional characteristics were maintained and the friction coefficient of the bearing was reduced by approximately one-third.
Abstract
- A research group—consisting of Masahiro Goto, distinguished chief researcher, Center for Green Research on Energy and Environmental Materials, NIMS; Michiko Sasaki, postdoctoral researcher, Center for Materials Research by Information Integration, NIMS; Masahiro Tosa, group leader, Research Center for Structural Materials, NIMS; Kazue Kurihara, professor, and Motohiro Kasuya, assistant professor, Institute of Multidisciplinary Research for Advanced Materials, Tohoku University—developed a coating technique using a zinc oxide (ZnO) material, an environment-friendly, low-friction material developed exclusively by NIMS. When bearing balls were coated with the ZnO material, the material’s low frictional characteristics were maintained and the friction coefficient of the bearing was reduced by approximately one-third. Moreover, the research group and Fox Corporation jointly developed a small jet engine generator for emergency use. By integrating the ZnO-coated bearings into the generator, its fuel consumption was reduced by 1%.
- In consideration of worsening global environment/energy issues, it is important to reduce friction occurring in drive mechanisms including engines in terms of energy saving. However, because the mechanically driven part in an engine becomes extremely hot, friction reduction technology applied in such an environment must be heat resistant. We focused on ZnO, capable of both reducing friction and resisting heat, and identified its friction reduction mechanism at the nano level. Then, we developed a basic technique to apply a low-friction ZnO coating by controlling the crystal orientation of ZnO.
- In efforts to put the developed basic technique to practical use, we applied the technique to reduce the friction level of commercially-available, high-performance bearings to an even further extent. We developed the technique for applying ZnO coating to bearing balls while controlling the crystal orientation of the ZnO material by rotating bearing balls in cage-shaped sample holders. As a result, we succeeded in reducing the friction coefficient of the bearings by approximately one-third. In addition, we integrated the resulting bearings into a small jet engine, evaluated its performance, and observed a 1% reduction in fuel consumption. Furthermore, we worked to miniaturize generators to be used in times of emergency when procurement of fuel is difficult. In this effort, we succeeded in developing a small jet engine generator equipped with ZnO-coated bearings. It weighs only about 40 kg, and can be carried by two adults. This compact generator, however, can produce 8,000 W of power, which can approximately cover the amount of power consumed by two households, and will be made available for emergency use.
- The newly developed low-friction ZnO coating is expected to be applicable not only to bearings but also to any mechanically driven parts that require friction reduction, given that the coating is usable in a wide range of conditions: from room temperature to high temperature, in oil, in vacuum and in atmosphere. By applying this coating technology to different types of mechanically driven parts in systems such as automobiles, it may be possible to save energy in these systems.
- This study was conducted in line with the university-led green innovation project “Green Network of Excellence (GRENE)” sponsored by the Ministry of Education, Culture, Sports, Science and Technology. More specifically, this study was carried out in accordance with the "Green Tribology Innovation Network" project (Principal investigator: Professor Kazue Kurihara, Tohoku University) within a GRENE category, the “Advanced Environmental Materials.” We will give a presentation on this study on August 5, 2016, during the PRICM9 meetings to be held in Kyoto.
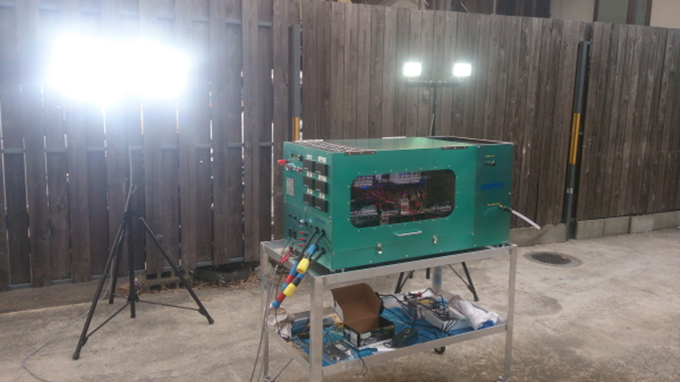
Figure: Small jet engine generator equipped with ZnO-coated bearings for emergency use (Lights in the back are being turned on using the power produced by the generator)
Related files
- Center for Green Research on Energy and Environmental Materials
- Center for Materials Research by Information Integration
Contacts
(Regarding this research)
-
Masahiro Goto
Distinguished Chief Researcher, Thermoelectric Materials Group, C4GR, NIMS
TEL: +81-29-859-2746
E-Mail: GOTO.Masahiro=nims.go.jp
(Please change "=" to "@") -
Kazue Kurihara
Professor, Insitute of Multidisciplinary Research for Advanced Materials,
Tohoku University
TEL: +81-22-217-6152
E-Mail: kurihara=tagen.tohoku.ac.jp
(Please change "=" to "@") -
Michiko Sasaki
Postdoctoral Researcher, Thermal Management and Thermoelectric Materials Group,
Materials research by Information Integration Initiative, NIMS
TEL: +81-29-851-3354
E-Mail: SASAKI.Michiko=nims.go.jp
(Please change "=" to "@")
(Regarding public relations)
-
Public Relations Office
National Institute for Materials Science
1-2-1 Sengen, Tsukuba, Ibaraki, 305-0047, JAPAN
TEL: +81-29-859-2026,
FAX: +81-29-859-2017
E-Mail: pressrelease=ml.nims.go.jp
(Please change "=" to "@") -
Administrative Office
Insitute of Multidisciplinary Research for Advanced Materials,
Tohoku University
TEL: +81-22-217-5204
FAX: +81-22-217-5211
E-Mail: soumu=tagen.tohoku.ac.jp
(Please change "=" to "@")