Increasing High-Temperature Strength of Materials Through Collaborative Efforts of AI and Materials Researchers
—Optimizing Thermal Aging Schedules by Analyzing the Unconventional AI-driven Outcomes—
2023.09.25
National Institute for Materials Science (NIMS)
A materials research team consisting of NIMS and Nagoya University has designed a novel two-step thermal aging schedule capable of fabricating nickel-aluminum (Ni-Al) alloys that are stronger at high temperatures than Ni-Al alloys fabricated using conventional thermal aging processes.
(”Artificial Intelligence Inspired Design of Non-Isothermal Aging for γ - γ' Two- phase Ni-Al Alloys” Vickey Nandal, Sae Dieb, Dmitry S. Bulgarevich, Toshio Osada, Toshiyuki Koyama, Satoshi Minamoto, Masahiko Demura; Journal: Scientific Reports [August 4, 2023]; DOI : 10.1038/s41598-023-39589-2)
Abstract
- A materials research team consisting of NIMS and Nagoya University has designed a novel two-step thermal aging schedule (i.e., non-isothermal aging or unconventional heat treatment) capable of fabricating nickel-aluminum (Ni-Al) alloys that are stronger at high temperatures than Ni-Al alloys fabricated using conventional thermal aging processes. This was achieved by using artificial intelligence (AI) techniques to identify several dozen different thermal aging schedules potentially effective in increasing alloys’ high-temperature strength. The mechanisms behind these schedules were then elucidated through detailed analysis. These results suggest that AI can be used to generate new insights into materials research.
- Ni-Al alloys are composed of a γ/γ´ (gamma/gamma prime) two-phase microstructure. Increasing the high-temperature strength of these alloys requires optimizing both the size and volume fraction of the γ´ phase formed within the alloy during the thermal aging process. These two parameters are determined by the conditions under which alloys are thermally aged (i.e., temperatures used and periods during which they are maintained). There is an enormous number of possible temperature-duration combinations. For example, dividing a thermal aging process into 10 equal intervals with nine predetermined aging temperatures results in approximately 3.5 billion (910) possible temperature-duration combinations. Because of this vast number of possible combinations, previous efforts to determine optimum thermal aging schedules had been limited to using constant temperatures. This research team previously succeeded in significantly reducing the time and cost needed to evaluate these combinations by shifting their approach from experiments to computational simulations. Still, the team found it unrealistic to simulate all 3.5 billion combinations.
- The research team recently adopted a Monte Carlo tree search (MCTS) system—an AI algorithm capable of streamlining a huge number of potential combinations into a smaller number of optimum ones. Using the MCTS algorithm, the team identified 110 thermal aging schedule patterns able to produce better results than conventional isothermal aging processes. The team initially found these patterns to be complicated and completely different from conventional isothermal aging, as shown in the figure. However, detailed analysis revealed the underlying mechanisms behind these patterns: initially aging a sample at a high temperature for a short period of time allows γ´ precipitates to grow until they reach near-optimum sizes, and subsequent low-temperature aging for a long period of time increases their volume fraction while preventing them from growing too large. Based on this discovery, the team designed a two-step thermal aging schedule—short-duration high-temperature aging to start followed by long-duration low-temperature aging. This schedule was proven to produce Ni-Al alloys that were stronger at high temperatures than those produced using any of the thermal aging patterns identified to be effective by the AI algorithm.
- In future research, the research team hopes to increase the high-temperature strength of more complex nickel-based superalloys already in practical use in gas turbines using this AI-based technique, thereby improving their efficiency.
- This project was carried out by Masahiko Demura (Director, Research Network and Facility Services Division (RNFS), NIMS), Satoshi Minamoto (Materials Data Platform Deputy Director, RNFS, NIMS), Vickey Nandal (Postdoctoral Researcher, NIMS), Sae Dieb (Researcher, NIMS), Toshio Osada (Principal Researcher, Research Center for Structural Materials (RCSM), NIMS), Dmitry S. Bulgarevich (Special Researcher, RCSM, NIMS) and Toshiyuki Koyama (Professor, Nagoya University).
This work—conducted under the structural materials DX-MOP framework—was supported in part by an SIP (Cross-ministerial Strategic Innovation Promotion Program) project entitled “Materials integration for revolutionary design system of structural materials.” - This research was published in Scientific Reports (Vol. 13, article number 12660) on August 4, 2023.
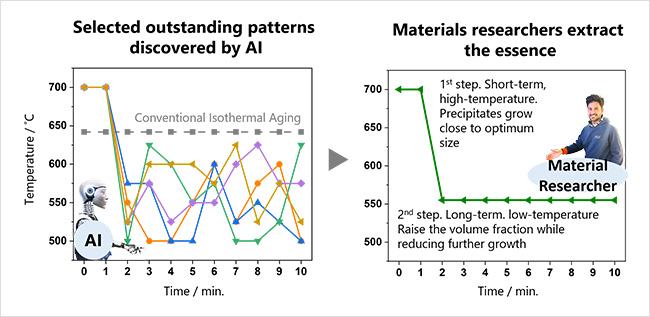
Figure. Novel two-step thermal aging schedule (right) designed by the materials research team with the assistance of AI tools
Related files
- Research Network and Facility Services Division (RNFS)
Contact information
(Regarding this research)
-
Masahiko Demura
Director
Research Network and Facility Services Division
National Institute for Materials Science
Tel: +81-29-860-4847
E-Mail: DEMURA.Masahiko=nims.go.jp
(Please change "=" to "@")
(General information)
-
Public Relations Office
National Institute for Materials Science
Tel: +81-29-859-2026
Fax: +81-29-859-2017
E-Mail: pressrelease=ml.nims.go.jp
(Please change "=" to "@")