Fatigue Cracking Mechanism in Metals Revealed through High-Resolution Three-Dimensional Imaging of Large-Volume Samples
—Technique May Help Enhance the Reliability of Aircraft Engine Components—
2022.10.28
National Institute for Materials Science (NIMS)
NIMS research team has identified the mechanism by which microscopic fatigue cracks grow in metals, solving a half-century-old mystery.
(”Three-dimensional high-resolution crystallographic observation of the entire volume of microstructurally small fatigue cracks in Ni-Co based superalloy” Hideaki Nishikawa, Yoshiyuki Furuya, Toshio Osada, Kyoko Kawagishi, Toru Hara; Journal: Scripta Materialia [September 5, 2022]; DOI : 10.1016/j.scriptamat.2022.115026)
Abstract
- A National Institute for Materials Science (NIMS) research team has identified the mechanism by which microscopic fatigue cracks grow in metals, solving a half-century-old mystery. The team found that these cracks grow along the slip planes of metallic crystals through three-dimensional imaging of large-volume samples. Most cracks were found to be caused by a shearing force rather than the tensile forces previously thought to be responsible.
- Metals experience fatigue fracture after being repeatedly subjected to external forces. Because this type of fracturing is a major cause of machine failure, understanding its mechanisms through research is important. Microscopic cracks initiate and grow in fatigued metals before they finally fracture. The crack growth mechanisms in the early and late fatigue life stages (i.e., when cracks have grown large) were identified more than five decades ago. However, the mechanisms by which microscopic cracks grow during the intermediate fatigue stage had been unclear, even though this represents the majority of fatigue life. The difficulty of observing cracks of about 200 μm in length was one reason.
- This research team recently developed an electron microscope-based analytical technique capable of high-resolution, three-dimensional crystallographic imaging of a large-volume metallic sample (100 times larger than the volume observable using conventional methods). This was the first time that fatigue cracks of approximately 200 μm in length were imaged three-dimensionally at high resolutions. This was achieved by applying the technique to a heat-resistant superalloy developed for use in aircraft engines. The team analyzed this image across the large sample and quantitatively determined the relationship between crack growth paths and crystalline orientations, leading to the discovery of a crack growth mechanism that differs from the mechanism conventionally assumed.
- Fatigue life management and prediction of metallic materials have been performed based on known fatigue fracture mechanisms. A more detailed understanding of these mechanisms would increase the accuracy of such predictions—particularly vital to the development and practical use of safer aircraft materials. The results of this research may help enhance the reliability of Japanese-made alloys and promote their practical use.
- This project was carried out by Hideaki Nishikawa (Senior Researcher, Fatigue Property Group (FPG), Research Center for Structural Materials (RCSM), NIMS), Yoshiyuki Furuya (Leader of FPG, RCSM, NIMS), Toshio Osada (Principal Researcher, Superalloys and High Temperature Materials Group (SHMG), RCSM, NIMS), Kyoko Kawagishi (Leader of SHMG, RCSM, NIMS) and Toru Hara (Leader of the Microstructure Analysis Technology Group, RCSM, NIMS). This work was supported by the SIP (Cross-ministerial Strategic Innovation Promotion Program) program entitled, “Materials integration for revolutionary design system of structural materials,” overseen by the Japan Science and Technology Agency (JST). This research focused on the Ni-Co-based heat-resistant superalloy developed by NIMS for use in aircraft engine turbine discs.
- This research was published in the online version of Scripta Materialia (Vol. 222) on September 5, 2022.
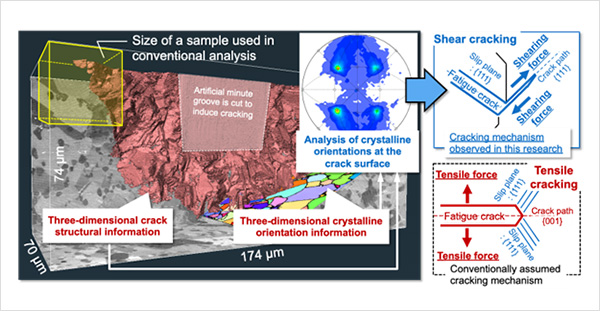
Figure. Three-dimensional imaging of a metal sample with a fatigue crack (left) and the crack growth mechanism revealed in this research (upper right) as opposed to the conventionally assumed mechanism (lower right)
Related files
- Research Center for Structural Materials(RCSM)
Contact information
(Regarding this research)
-
Hideaki Nishikawa
Senior Researcher
Fatigue Property Group
Research Center for Structural Materials
National Institute for Materials Science
Tel: +81-29-859-2796
E-Mail: NISHIKAWA.Hideaki=nims.go.jp
(Please change "=" to "@")
(General information)
-
Public Relations Office
National Institute for Materials Science
Tel: +81-29-859-2026
Fax: +81-29-859-2017
E-Mail: pressrelease=ml.nims.go.jp
(Please change "=" to "@")