Press Release 2020
Achieving Cost-Efficient Superalloy Powder Manufacturing Using Machine Learning
—Technique Efficiently Optimizes Complex Manufacturing Processes and May Reduce Aircraft Engine Component Production Costs—
Japan Science and Technology Agency (JST)
High-performance, high-quality Ni-Co-based superalloy powders are promising aircraft engine raw materials. Using machine learning, a NIMS team has succeeded in speedily determining the optimum parameters for manufacturing these types of powders at high yields.
(”Machine learning-driven optimization in powder manufacturing of Ni-Co based superalloy” Ryo Tamura, Toshio Osada, Kazumi Minagawa, Takuma Kohata, Masashi Hirosawa, Koji Tsuda, Kyoko Kawagishi; Journal: Materials & Design (2020);[December 1, 2020]; DOI : 10.1016/j.matdes.2020.109290)
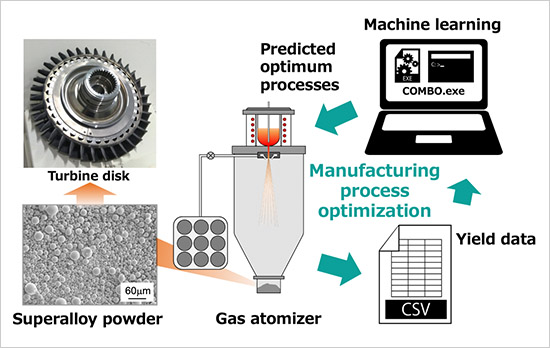
Figure 1. Optimization of superalloy powder manufacturing processes using machine learning
Metal 3D printing has been rapidly adopted in aerospace engine production, leading to growing demand for low-cost manufacturing and supply of the alloy powders these printing techniques require. When these materials are used in the production of high-pressure turbine disks—a core engine component—they need to meet particularly rigorous requirements: they have to be heat-resistant, highly plastic, high-quality and homogeneous superalloy powders that can be processed into spheres. They also need to be produced at high yields to reduce costs. In practical manufacturing settings, superalloy powders are commonly produced for this purpose using large gas atomizers. It is therefore important to optimize a number of manufacturing parameters, such as the temperatures used to melt metals and the gas pressures. However, this optimization process has proven to be enormously costly, time-consuming and labor-intensive even with the assistance of knowledgeable and experienced experts.
This research team used machine learning in an attempt to optimize gas atomization processes for the manufacturing of Ni-Co-based superalloy powders suitable for high-pressure turbine disk production without relying on the knowledge of experts. As a result, the team succeeded in manufacturing fine-grained powders that can be processed into spheres. In addition, use of the parameters dramatically increased production yields from the conventional 10-30% to approximately 78% after performing experiments only six times without using previously collected data. The powder manufactured in this research was approximately 72% cheaper than commercially available powders when the prices of the raw materials were compared.
After years of R&D, NIMS has developed techniques for designing superalloys with controlled physical properties, such as heat resistance. The combined use of these techniques and the parameter optimization technique developed in this research is expected to enable low-cost production of functional superalloy powders designed to meet specific purposes. The prediction accuracy of machine learning models increases as they receive more training data. Superalloy powder manufacturers in the private sector possess largely unexploited manufacturing process data. Integrating this data may further improve the ability of our technique to predict optimum parameters, potentially enabling the manufacturing of higher-quality powders at lower cost.
This project was carried out by Ryo Tamura (Senior Researcher, First-Principles Simulation Group, International Center for Materials Nanoarchitectonics, NIMS), Toshio Osada (Principal Researcher, Superalloys and High Temperature Materials Group (SHTMG), Research Center for Structural Materials (RCSM), NIMS), Kazumi Minagawa (Special Researcher, SIP-MI Laboratory, Research and Services Division of Materials Data and Integrated System (MaDIS), NIMS), Takuma Kohata (Engineer, SHTMG, RCSM, NIMS), Masashi Hirosawa (Engineer, SHTMG, RCSM, NIMS), Koji Tsuda (Invited Researcher, MaDIS, NIMS) and Kyoko Kawagishi (Leader of the SHTMG, RCSM, NIMS).
This project was supported in part by the SIP (Cross-ministerial Strategic Innovation Promotion Program) program entitled “Materials integration for revolutionary design system of structural materials” managed by the Japan Science and Technology Agency (JST).
This research will be published in Materials & Design, an open access journal, on December 1, 2020, Japan Time.
(Regarding this research)
Ryo Tamura
Senior Researcher,
First-Principles Simulation Group,
Nano-Theory Field, MANA, NIMS
Tel:+81-29-860-4948
E-Mail:TAMURA.Ryo=nims.go.jp
(Please change "=" to "@")
Toshio Osada
Principal Researcher,
Superalloys and High Temperature Materials Group,
Design and Producing Field, NIMS
Tel:+81-29-859-2208
E-Mail:OSADA.Toshio=nims.go.jp
(Please change "=" to "@")
Kyoko Kawagishi
Group Leader,
Superalloys and High Temperature Materials Group,
Design and Producing Field, NIMS
Tel:+81-29-859-2314
E-Mail:KAWAGISHI.Kyoko=nims.go.jp
(Please change "=" to "@")
(Regarding the SIP program “Materials integration for revolutionary design system of structural materials”)
Katsuhiko Takahashi
SIP Group, Department of Innovation Platform,
Japan Science and Technology Agency
Tel:+81-3-6261-0013
Fax:+81-3-5214-8496
E-Mail:sip-material=jst.go.jp
(Please change "=" to "@")
(General information)
Public Relations Office
National Institute for Materials Science
Tel:+81-29-859-2026
Fax:+81-29-859-2017
E-Mail:pressrelease=ml.nims.go.jp
(Please change "=" to "@")
Public Relations Division
Japan Science and Technology Agency
Tel:+81-3-5214-8404
Fax:+81-3-5214-8432
E-Mail:jstkoho=jst.go.jp
(Please change "=" to "@")