Joint Workshop LANL/NIMS Quantum and Functional Materials and MANA International Symposium 2024
Nanomaterials - 13
Abstract
Polycaprolactone (PCL)-based scaffolds, fabricated using 3D printing, have gained attention in bone tissue engineering due to their biocompatibility, biodegradability, and precise geometry control. However, tuning the mechanical properties and hydrophilicity of the scaffold to meet the specific requirements for bone tissue application remains a challenge. Fullerene (C60) has recently emerged as a promising filler in composite materials due to its excellent mechanical properties. In this study, we explored self-assembled C60 nanorods (FNR) and pluronic 123 surface-modified C60 nanorods (PFNR) as reinforcing fillers in the PCL scaffold. The incorporation of 0.013 wt% FNR showed enhanced mechanical properties compared to the pure PCL scaffold, without significant changes in the hydrophilicity. In contrast, incorporating PFNR in PCL scaffolds not only improved the mechanical properties but also enhanced the hydrophilicity. As a result, the scaffold showed excellent proliferation activity of Human Wharton's Jelly Mesenchymal Stem Cells. Moreover, both the FNR and PFNR-incorporated PCL scaffolds showed antibacterial properties essential to prevent implant-associated infections. This study demonstrates that the mechanical properties and hydrophilicity of PCL scaffold can be tuned by adjusting the type and concentration of fillers, optimizing cell proliferation and antibacterial activity for potential applications in bone tissue engineering.
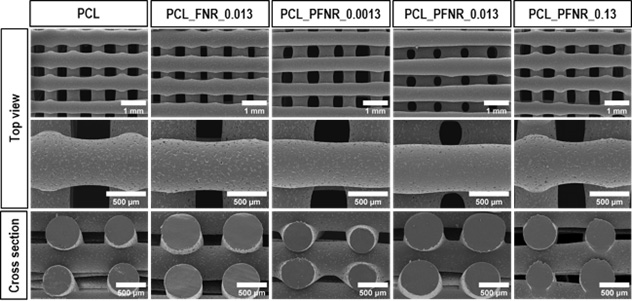
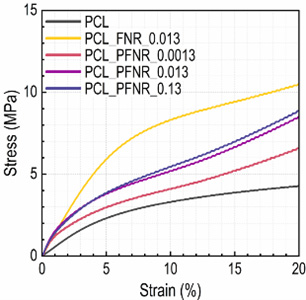
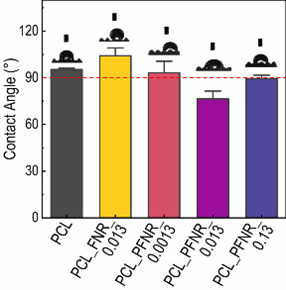
Reference
- C. W. Wong. et al, Nanoscale 14, 11152 (2022), DOI 10.1039/d2nr01817a
- M. Mira. et al. Mater Adv 4, 6407 (2023), DOI 10.1039/D3MA00332A