Melting-Casting Furnace for Structure Control
This apparatus consists of three parts for each process, that is, melting furnace, water-cooling copper mold for casting and water spray-zone. Continuous experiments through melting, deoxidation, casting, and cooling with various experimental conditions can be conducted by using this apparatus, and the effect of composition of molten steel, kind of inclusion, and solidification or cooling rate on microstructures of casting can be investigated.
|
* Melting Furnace
Induction heating furnace with MgO crucible inside of the copper crucible whose capacity is 35kg by iron |
Specification
Power : 150kW
Frequency
Inner Diameter(Crucible): 180mm
Maximum Capacity :35kg(iron)
Atmosphere: Ar
|
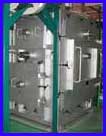
|
* Casting Mold
Induction coil surrounding the mold for heating to control the solidification rate
* Water Spray Zone
water spraying with canging time for various cooling rate
|
Specification
(Mold)
Capacity:8kg(iron)
Wall:Water-Cooling Copper
(Heating Device)
Power : 250kW
Frequency
Atmosphere: Ar
Cooling Method: Water spray
|
Shear Added-Rolling Simulator
This rolling mill is able to introduce both compressive strain and shear strain. Conventional rolling, cross roll rolling, and differenct speed rolling is possible.
By using Shear Added-ROlling Mill, grain size, texture, mechanical properties of rolled place and so on are different from those in case of conventional rolling.
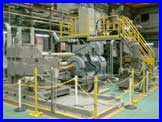
|
* Cross roll rolling:
Share strain through plate thickness by making upper and lower roll intersect. Maximum cross angle is 10 degrees.
* Different speed rolling:
The share strain through place thickness by changing upper and lower roll velocity.
|
Specification
Mill type: Cross 2 high mill Work roll: 400 x 300
Maximum rolling force:300ton
Drive motor 1 : DC300kW
Drive motor 2 : DC150kW
Maximum rolling speed:30m/min
Cross angle
|
Multidirection Drformation Thermomechanical Treatment Simulator
Multi axis processing is an effective method for the refinement of the grains and the randomization of the texture. This machine can process a series of the rotating and forging specimens.
It is possible to forge into a different direction at each process. We examine the relation between the multi functional processing and the refinement or the texture of the grains.
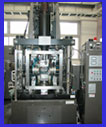
|
* Mechanisms
This machine has the following three mechanisms and can simulate the rolling and forging process.
(1) Processing mechanismwhich used two hydraulic Actuators (Maximum lead 25 ton/ Maximum speed 2m/s)
(2) Heating mechanism which used direct energizing and high frequency electricity heating.
(3) Mechanism which rotates the specimen
|
Characterization Equipment for Deformed Crystalline Microstructure
Multifunctional Microstructure Characterization Equipment Composed of Scanning Electron Microscope (SEM), Orientation Imaging Microscope (OIM) and Energy Dispersion Spectroscopy (EDS).
EBSP (Electolon Bac-Scattering diffraction Pattern) appears as the result of the interaction of incident electron beam and crystalline material. The orientations of micro-scale regions can be obtained and the crystal orientation and phase distribution in the materials can be mapped and analyzed. Meanwhile, the element distribution in the materials is characterized quantitatively with EDS.
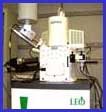
|
Orientation Imaging Microscope
(TexScanLaboratory, USA)
DVC 1612 CCD Camera
OIM analysis 3 Software Package
Energy Dispersion Spectroscopy
Hi-Re Sapphire Detector
Genesis Software package
|
Specification
Scanning Electron Microscope
LEO1550 GEMINI (Carl-Zeiss, Germany
Shottcky FE-Gun 30 V-1nm Resolution
|
|